Making the Switch to Condensing Boilers
August 11, 2014
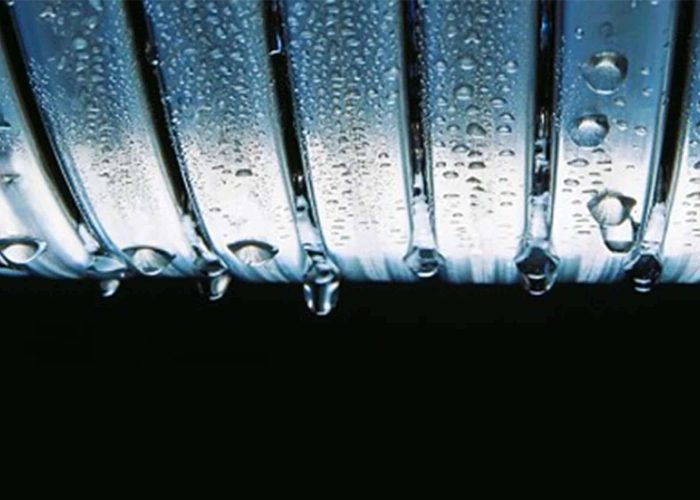
Condensing boilers have the capacity to shrink energy consumption, take advantage of utility provider incentives, and save money for your building, but how do they really work? What makes them different from a traditional boiler? Investing in a modern condensing boiler has the potential to yield significant savings, and here’s why you should consider the switch.
Before understanding the science and benefits behind a condensing boiler, it is important to revisit how a “conventional” boiler works. A traditional wetback fire tube boiler has a burner that sends a flame into a furnace. Hot flue gases pass through tubes that are surrounded by water. This is called the heat exchanger. The water is heated and then circulated throughout the building. The flue gases and byproducts of combustion are removed from the building through a chimney.
The efficiency of a boiler is gauged by measuring how effectively the heat generated by burning a fuel source is transferred to the water in the boiler, as well as how much heat is rejected and lost into the atmosphere. At the end of the day, if you are paying $1.00 for a therm of natural gas, how much of that is actually going towards its intended purpose: heating your building. Running an inefficient boiler is literally like burning money. Expensive heat energy is disappearing through the chimney as those emissions are sent into the atmosphere. This is where the challenge presents itself. Perhaps the heat exchanger or the guts of the boiler can be configured differently to gain more thermal efficiency. For the most part, traditional non-condensing boilers all perform similarly, given that their heat output is really just a byproduct of the energy in the fuel being released through combustion.
We recall from chemistry class that methane (CH4) and oxygen (O2) react to form CO2 + H2O + heat in the process of combustion. We also know that the byproduct water turns to steam at 212°F. The amount of energy it takes to raise the temperature of 1 lb of water by 1°F is known as a British Thermal Unit (BTU). It takes 1,000 times that amount of energy to change the phase of that pound of water from a liquid to a gas at 212°F. This is known as the latent heat of vaporization. That is why water on the stove heats up to 212°F quickly but takes longer to reach a rolling boil. The water needs to absorb energy (heat from the boiler or stove), in order to spread the molecules out in a gaseous form (steam). The same process works to cool you down and is known as perspiration. Sweat absorbs heat from your skin, leaves your skin through pores, and evaporates to cool down the body.
The most significant component of increased efficiency, when using condensing boiler, happens through releasing latent heat from the flue gases by…condensing. For a standard 80% efficient boiler, flue gases can be between 300°F and 400°F. In order to drive boiler efficiency up to the 90% range, the flue gases need to be cooled to below their dew point temperature of 130°F. This is accomplished by lowering the water temperature entering the boiler. Considering that the interior space will be around 70°F, the water in the heating system will typically be above that. Because of this constraint, there is a practical upper limit to the boiler efficiency that can be realized. While 100% efficiency is always desired, the water would have to be cooler than could ever happen in practice. The figure to the right illustrates the condensing point, as well as the temperatures required for near 100% efficiency
While lowering the boiler inlet temperature does not appear to be a difficult change to make in itself, doing so can wreak havoc on a traditional boiler. As water condenses out of the flue gas, it will react with carbon and sulfur in the fuel to form an acid that will eat away at the heat exchanger. To overcome this damaging effect, condensing boilers have the tubes in the heat exchanger constructed out of corrosion resistant materials like stainless steel. This is more expensive and the reason for the cost premium on high efficiency condensing boilers. Realized energy savings and utility rebates/incentives will help to offset the higher capital investment.
Unfortunately, installing a condensing boiler on its own will not solve all of your heating challenges. The hot water coils (see image below) located in air handling units throughout the building were designed to operate at a specific temperature – typically ~180°F. Decreasing the temperature of the water from the boiler (to gain the energy efficiency advantages of condensing) will have a downside: it will certainly affect the performance of the coils. Heating equipment should, therefore, be evaluated as a total system to determine what other alterations need to be made, beyond changing to a condensing boiler. These wider system upgrades could certainly limit the Return on Investment of a new condensing boiler.
Whatever your specific situation, conducting a thorough assessment will determine the potential energy savings associated with switching to a condensing boiler, while also identifying any further work that may be required. Regardless, switching to condensing boilers may be the first step to ensure that your money doesn’t go up in smoke.