Hamilton Southeastern School District is one of the largest school districts in Indiana with an estimated 21,000 students and 21 school buildings. In 2009, the District was experiencing high energy costs and comfort issues in the classrooms, including loud noise, temperature fluctuations, and uneven air distribution. With a focus on improving the learning environment and reducing electric and gas utility costs, the District implemented a guaranteed energy savings project that produced more than $8.7 million in energy cost savings in five years with a project cost of just $3.7 million—a dramatic net savings of $5 million.
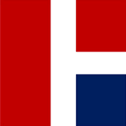
“When we decided to pursue an energy savings project, we set an aggressive goal of saving $1 million on an annual basis. Performance Services was able to exceed that goal even with the complexity of our HVAC and control systems. We are extremely pleased with the quick payback of this project. Our utility costs are significantly lower and we have an improved learning environment.”
Director of Facilities
The project proved to be particularly significant in terms of saving energy at Fishers High School. Newly constructed in 2002, the annual utility bill at the school averaged more than $816,000 and the building was 63% less efficient than most schools of its size and type before an energy savings project with a baseline energy use index (EUI) of 117.9 or 117,940 BTUs per square foot.
Energy Conservation Measures
After a detailed energy audit, the District elected to retrofit Fishers High School’s constant volume air system with a variable air volume (VAV) system to reduce electrical usage and improve airflow and comfort. A new high-efficiency Jockey boiler was installed to reduce gas usage and cost. The engineer also confirmed that the existing air handling unit (AHU) fan motors were variable frequency drive (VFD) compatible. Variable speed frequency drives were then added onto two air handlers along with duct static pressure sensors. The VFDs and sensors reduce electric usage by controlling the fan speed on the AHUs. This allows the motors to run more efficiently at varying speeds instead of at a constant speed.
Reprogramming the Building Controls
After installing the energy conservation measures, the engineer reprogrammed the current building control system, including modifying the way the hot water, chilled water, and air ventilation systems ran. The hot water system was programmed to include the new high-efficiency boiler which could run if necessary during the fall and spring seasons. The new boiler would only run if the indoor air temperatures were too low and the outside temperature was cold. The system program also ensured that the boiler did not operate during warm weather unless absolutely necessary, saving on natural gas cost.
An optimal start time was also added to the system schedules. This feature allows equipment to start early, to assure classrooms reach the desired temperature setpoint by the scheduled start of school. The amount of time it takes for the classroom to reach the temperature set point varies and is dependent on the outside air temperature. If the weather is cold, the system can turn on up to two hours early to ensure spaces reach the desired temperature. If the weather is mild, the system can adjust its start time to just 15 minutes early.
The optimal start saves energy and cost because maintenance staff does not need to manually set early start times each day in order to guarantee classrooms are the right temperature by the start of school. When maintenance would set early start times prior to the use of optimal start, the ventilation system would bring in outside air while trying to heat or cool the classrooms. Bringing fresh air into the classroom is critical to the learning environment but is only necessary when students and staff are present. Outside air must be heated or cooled when being brought into the building which uses energy. During optimal start, outside air is not brought into the building until it is needed and students are in the classrooms, which makes the building much more efficient.
The engineer also added CO2 control to the building automation system. CO2 sensors ensure the right amount of outside air was being brought in to keep CO2 levels below 1,000 PPM and excessive amounts of fresh air were not being conditioned for classrooms and large group areas, which saves money and energy.
Additionally, the engineer found some existing issues with building automation controls programming at the school. The fan powered boxes that supply air to the classrooms were running 24/7, overheating spaces during unoccupied mode. The system would then enter cooldown mode in the morning, which caused low limit freeze protection nuisance alarms. Not only was this wasteful, it caused enormous comfort issues for the first part of the day as students and staff were arriving for the day.
By re-commissioning the control systems, optimizing the building sequences and installing new high-efficiency equipment, each classroom is now guaranteed an optimal learning environment. The majority of improvements were completed while school was in session with no disruption to the school schedule.
Energy Savings Results
The utility bill savings at Fishers High School totaled $320,362 and energy usage per square foot was reduced by an impressive 44% to 65,546 BTUs/sq. ft. or 65.5 EUI. In the first two years alone the school reduced usage of their utility bills by $597,385. The total cost of the Hamilton Southeastern Schools contract was $3,748.000 with achieved energy savings of $8,789,002 in just a five year period of time as evidenced through measured and verified gas and electrical utility bill tracking. The energy use index for the campus reduced by 25% from 96.5 to 72.6 for the entire campus—demonstrating that a building automation controls-focused project can have a dramatic impact on a school’s operating costs.
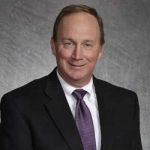
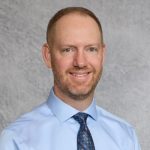